
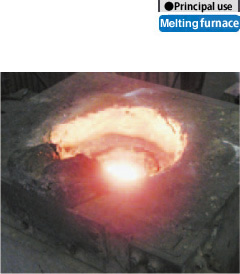
Contributing to stable induction furnace operation
for copper alloys.
Monolithic refractories for non-ferrous
(induction furnace for copper alloys)
- Ultimate refractories for induction furnace
melting copper alloys. - Line-up products to meet various operating
conditions. - Quality stability with our own quality control.
- Various installation by various.
■Characteristics |
Application | Product Name | Chemical compositions(%) | Installation Quantity (m3) |
Install- ation me- thod |
Kneading Water Quantity (%) |
Note | ||
---|---|---|---|---|---|---|---|---|
Al2O3 | SiO2 | SiC | ||||||
Coreless Induction furnace | DV-351A | 75 | 10 | 12 | 2,760 | D | - | |
Coreless induction furnace |
EDR-GS45 | 45 | 17 | 34 | 2,500 | D | - | |
Inductor for channel type induction furnace | MINRO-A282 | 88 | 4 | 4 | 3,180 | D | - | |
Inductor for channel type induction furnace |
EWR-A90 | 87 | 8 | - | 2,850 | R | - | |
Bath for channel type induction furnace | CASTIX-41Z | 39 | 58 | - | 2,150 | C | 7.5to8.5 | |
Bath for channel type induction furnace | CASTIX-620Z | 59 | 37 | - | 2,600 | C | 6to7 | |
Repair | Rac Coat P80 | 87 | 8 | - | 2,950 | P | - | Repair |
Furnace Lid / Atmospheric Application | MD-160 | 53 | 41 | - | 2,050 | C | 13to15 | General use |
Insulation・Back lining | MDL13N | 36 | 45 | - | 1,050 | C | 30to40 | Insulation |
Installation method D:Dry vibration, C:Casting, R:Ramming, P:Patching,
※These figures are typical values but not guaranteed values.
![]() |
■Crack repairing materialWet type mortar “Super 3000SW” is recommend- able for stronger bonding and repairing fine cracks. |
![]() |
|||||||||||||
■Air setting high alumina base mortar.
|