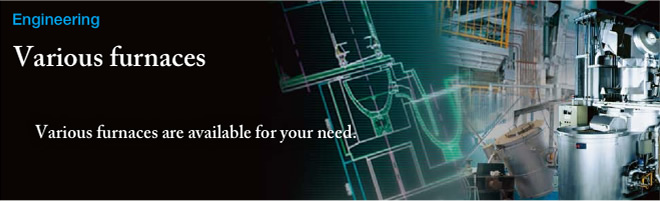
Break the bounds of common practice for melting furnace
Non-Oxidation Furnace 「Freedom」
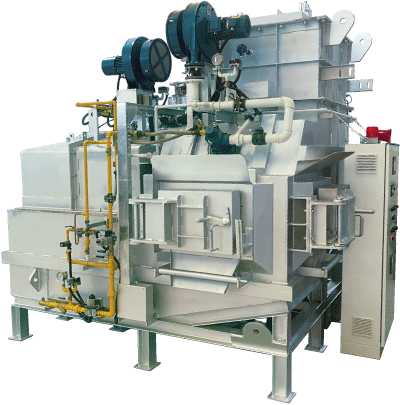
![]() |
Inside furnace(without cleaning for 6months) 3-5mm oxide film is formed on the molten metal surface but it is not hardened so that adhered dross on the furnace wall can be easily removed. |
- Reduce impurities due to less oxide (K mold method, Ranked A (K value<0.1))*1
- Lower ambient temperature in the furnace and hydrogen gas absorption to the molten metal will be less due to the oxide film formed on the metal surface. (0.2cc/100gAl or less) *2
- Reduce the temperature fluctuation because of the independent holding and melting chambers so that the tapping temperature will be kept within plus/minus 3ºC. *3
- Lower burden to the holding burner because the molten metal flows into the holding chamber at much the same temperature as the tapping. The thermal efficiency is 50% or more in conjunction with heat exchanger of the burner. (40% or less for conventional furnaces) *4
- Almost no cleaning of the holding chamber is required and less aluminum loss by the form of the dross. Achieve melting yield of 99% or more because of higher melting efficiency with less unmelted metal. *5
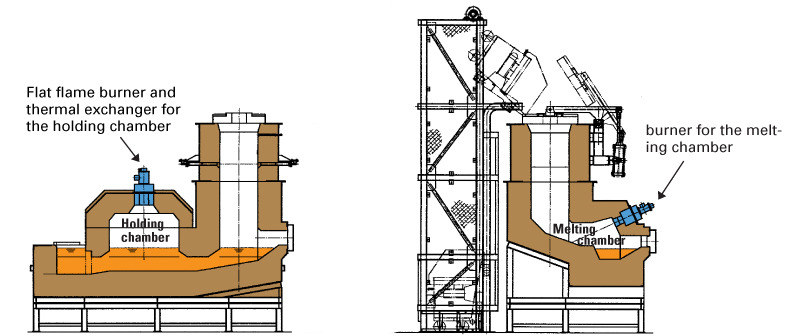
For conventional furnace, exhaust gas in a holding chamber discharged to the tower in a melting chamber but outside air also flows into the holding chamber. This is the same situation as heating a room with windows open. For Freedom, the holding chamber is independent and separated from the melting chamber. Outside air does not inflow to the holding chamber and this furnace can operate “with the window shut”. As a result, exhaust gas does not inflows mutually, which does not affect the oxygen concentration in the holding chamber. Also aluminum dross developed in the melting chamber does not inflow to the holding chamber because the dam at the inflow inlet prevents it from inflowing
Oxide is almost free for this furnace and does not cause excessive temperature rise because of no direct flame impingement to molten metal and without trembling the molten metal surface. In addition, the heat recovery is improved significantly with the thermal exchanger installed in the holding burner for the exhaust gas, which leads to further energy saving.
![]() |
Flat flame burner for the holding chamber |
The number of combustion air pipe is reduced by placing the blower with the burner, which results in flexibility of the layout and easy maintenance work.
![]() |
The first unit started operation in China August 2016. 59 units are under the operation in china and other countries.