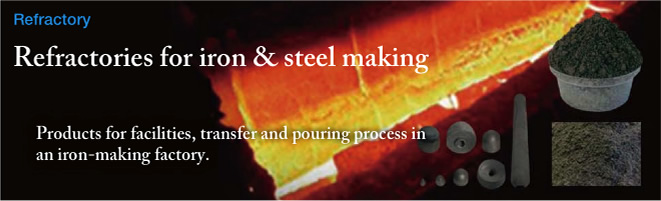
Trough Material
Our casting materials for a blast furnace main trough are silica free materials with a high thermal and
spalling resistance. Materials for an iron runner have an abrasion and FeO resistance. Materials for runners
that require a long time operation have a spalling and anti oxidation resistance, in addition to the
corrosion resistance. We offer various materials depending on the operation and working conditions.
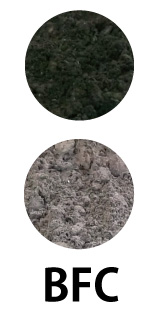
Properties |
Application | Chemical Composition(%) | |||||
---|---|---|---|---|---|---|
Al2O3 | MgO | SiC | SiO2 | C | ||
Main Trough | Metal Zone | 65 to 75 | 5 to 10 | 15 to 20 | 0 | 2 to 3 |
Metal Zone | 72 to 75 | - | 15to20 | 0 | 2 to 4 | |
Slag Zone | 12 to 30 | - | 60 to 76 | 0 | 2 to 5 | |
Runners | Iron runner | 55 to 70 | - | 20 to 35 | 1 to 3 | 2 to 3 |
Slag runner | 60 to 75 | - | 25 to 40 | 1 to 3 | 2 to 3 | |
Tilting Trough | Iron | 55 to 70 | - | 20 to 35 | 1 to 3 | 2 to 3 |
Iron(For disiliconization) | 90 | 5 | - | 1 | - | |
Slag | 60 to 75 | - | 25 to 40 | 1 to 3 | 2 to 3 |
Our ramming materials are manufactured by using our own technique called “The Advanced Mixing
Method”. In addition, clay with a high heat resistance and plasticity is used and it exhibits a superior
workability and a high corrosion resistance. We have various materials for the blast furnace market but
also for the foundry market.
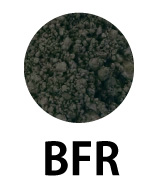
Properties |
Material | Alumina・Silicon Carbide ・Graphite Quality |
|
---|---|---|
Chemical Composition (%) | F.C. | 3 to 7 |
SiO2 | 3 to 10 | |
Al2O3 | 55 to 75 | |
SiC | 20 to 30 | |
Pressed Sample 1450℃ x 3Hr Sintering |
Compression Strength |
45 to 70 |
Modulus of Rupture |
5 to 10 |
|
Installation Quantity(kg/m3) Installation Quantity |
2600 to 2800 |